Do you know how glass is made? I had a chance to visit a glass factory and study all the stages of glass production.
Glass production begins with the receipt of raw materials. Most modern factories work on imported purified raw materials, which allows them not to build cleaning and separation shops on their premises. Often it is even more profitable. The raw material is shipped, and it is sent to hoppers for storage.
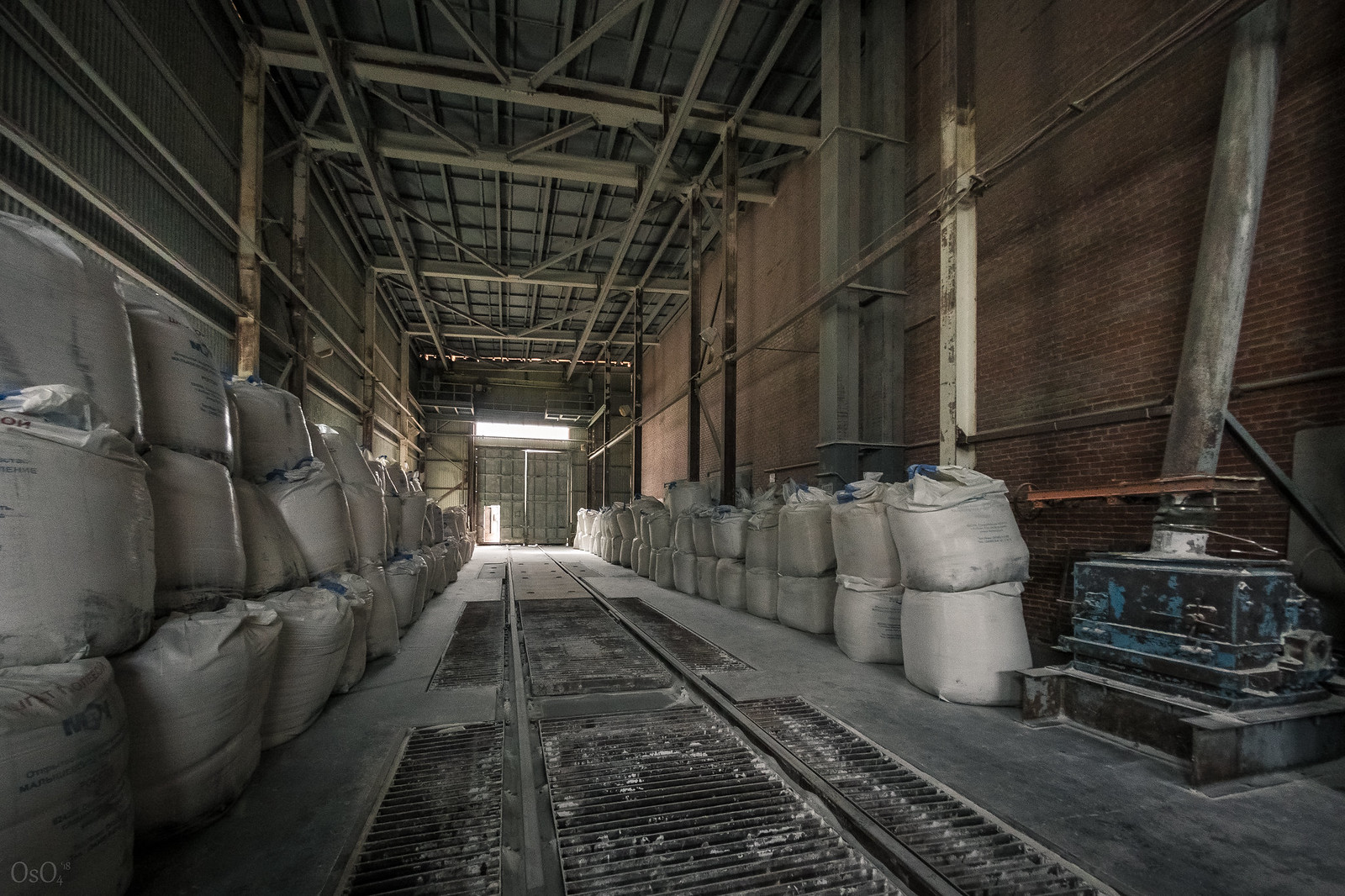
The general formula for glass is Na2O*CaO*6SiO2. It is very approximate and is supplemented by some other substances in production.
It is worth telling about the raw material used. It should have a constant particle size distribution and chemical composition and high purity, which will allow to obtain a homogeneous product with the desired properties. Since the first and second (but to a lesser degree) oxides in the glass formula are not chemically stable in the air, mineral products with the necessary oxides are added to the charge.
The substances used can be divided into main and auxiliary substances. The former is a mix of acid and basic oxides that form the basis of glass and determine its main properties.
Among these are:
Silicon oxide SiO2, aka silica. Crystalline and vein quartz and rock crystal are suitable raw materials, but in 99% of cases, silica sand is used. The content of SiO2 in the final product is over 70%. The quality of the sand is determined by its particle size and chemical composition. Good glass sand must contain not less than 95% silicon oxide, and without color impurities, for example, oxides of iron. We will talk about coloring impurities later.
Calcium oxide CaO is introduced in the form of calcite carbonates: calcite, limestone, chalk, and dolomite.
Sodium oxide Na2O - in the form of soda or sodium sulfate.
The latter auxiliaries are needed to improve the mechanical and optical qualities of glass, its resistance to crystallization, as well as to give it color!

Aluminum and boron oxides improve the mechanical properties. Oxides of lanthanum, thorium, and some other rare earth metals increase transparency and reduce distortion in optical glass.

Arsenic and antimony oxides and ammonium compounds are used as clarifiers: they evaporate in the glass melt and capture small air bubbles with them. Fluorine and phosphorus compounds give glass a milky opacity.

The oxides of many metals and some simple substances stain glass in different colors. Fe2O3 is brown, FeO is bluish, Cr2O3 is green, CoO is blue, CuO is red, Se is ruby, and UO2 is uranium green.

By the way, the Kremlin stars are made of selenium glass, also called selenium ruby.

Also, one of the components of the raw material mixture is broken glass, usually broken glass pieces, up to 20% of the total mass. They are either obtained by rejecting the finished product at the final stages, or the factory makes a batch of glass for the breaking, or the plant buys it somewhere.
All the glass components are weighed in the necessary quantities, mixed into a single homogeneous mass, called a batch, a little humidified (so as not to dust), and sent into the furnace.
So, the process begins! First, silica sand, the main component of glass, is poured in doses from hoppers on the conveyor.

This is what it looks like from below. This is the beginning!
The conveyor moves upwards, and gradually other components are added. Here the CaO is added.
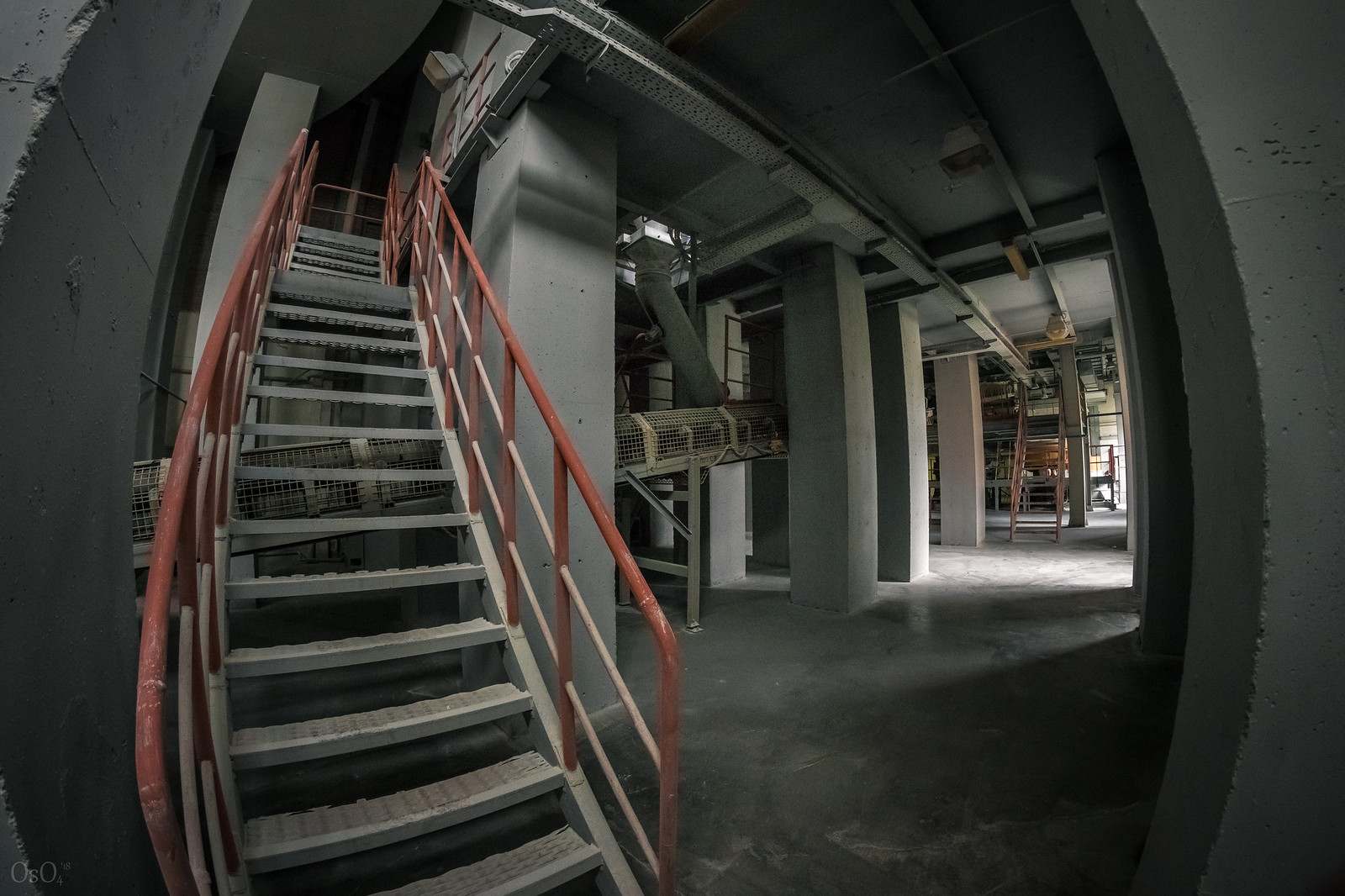
The same area from above. You can see the hoppers and the scales.
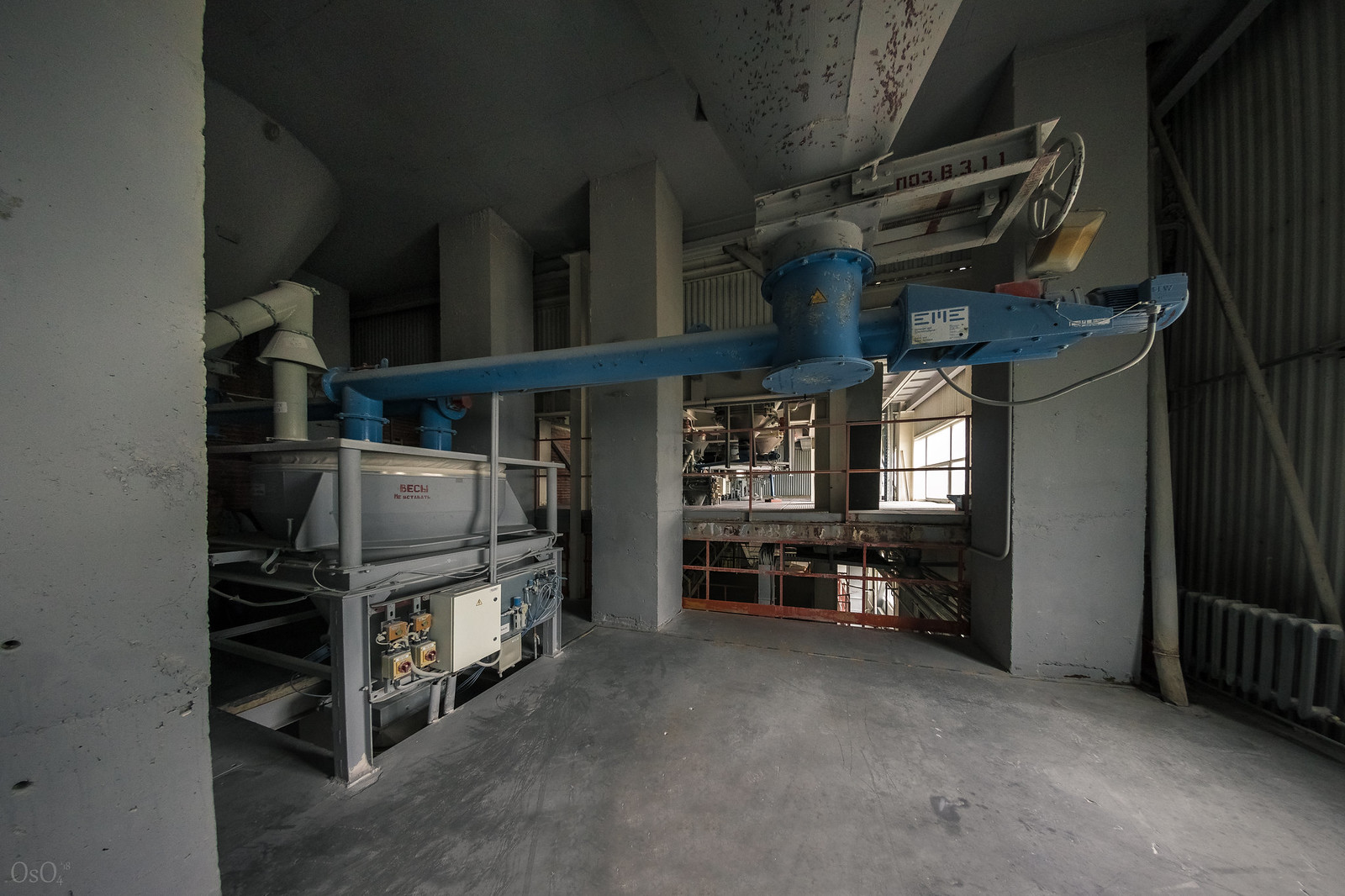
On the left for dolomite, on the right for limestone.
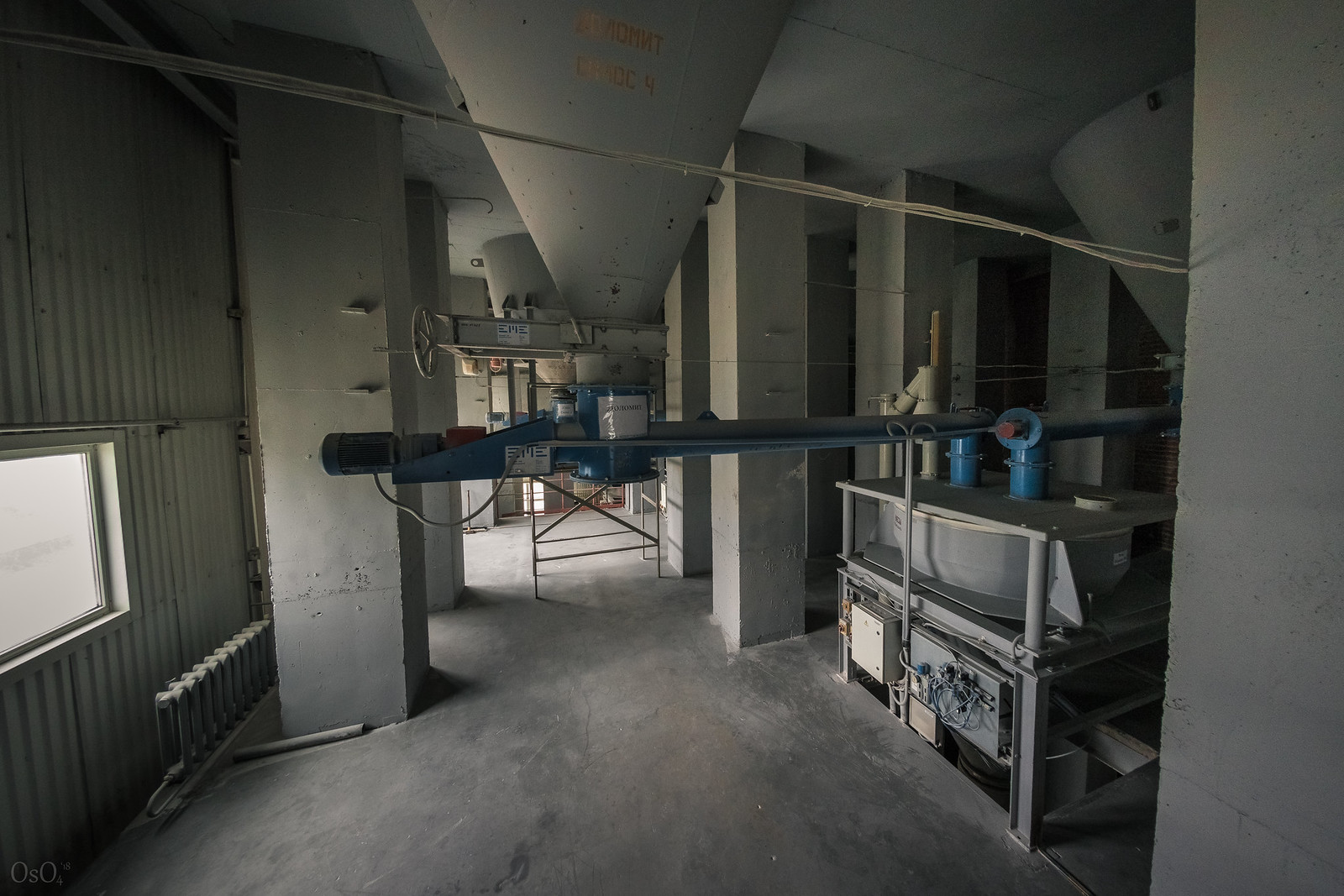
Moving on.
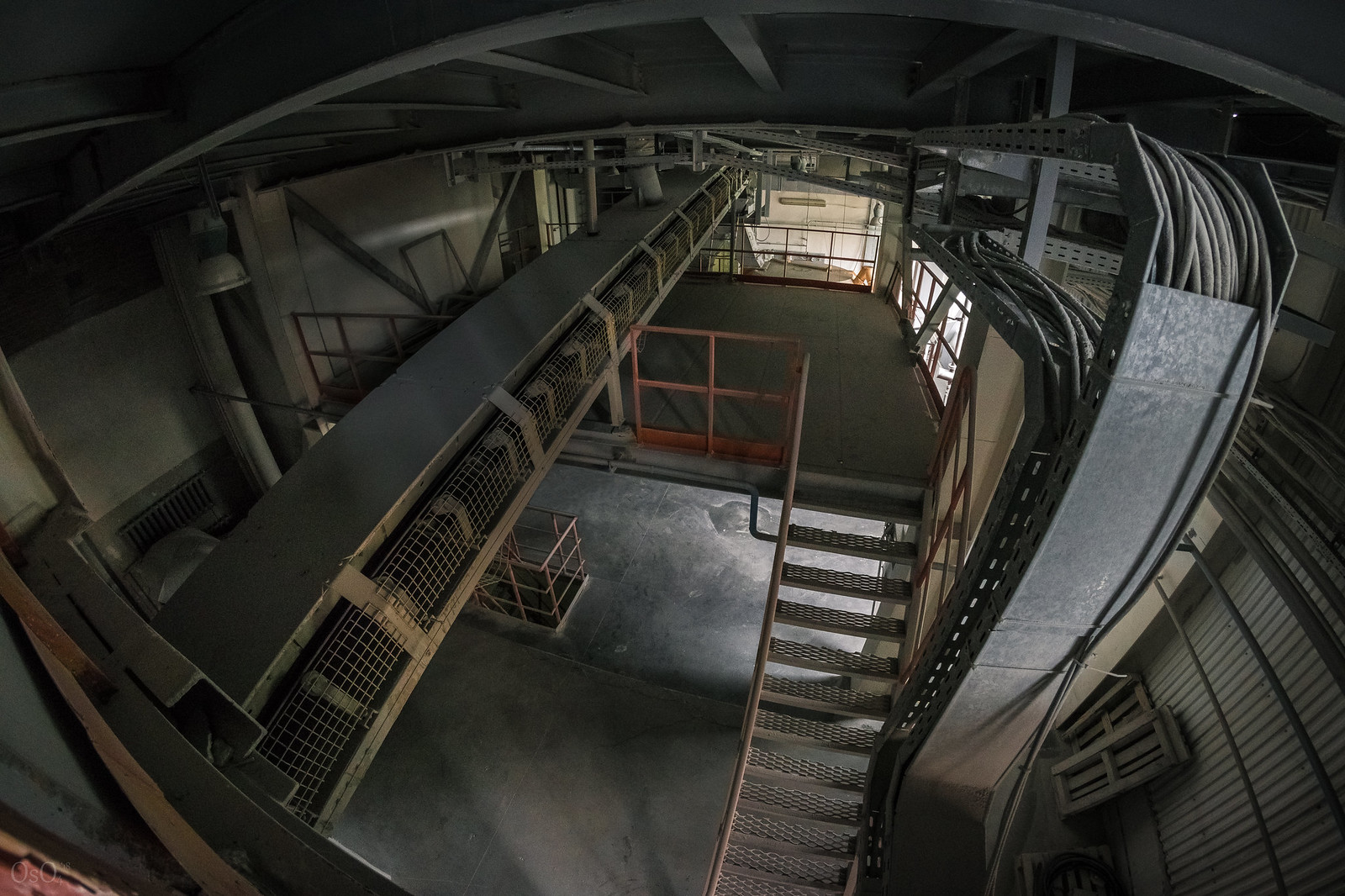
What is the last major component left? Did you read carefully? :) That's right, sodium carbonate. One of the four closest bins contains just that. The other three contain feldspar, sodium sulfate, and ammonium chloride. These three substances are the source of Al2O3 and K2O, an additional source of Na2O, and the main clarifier.
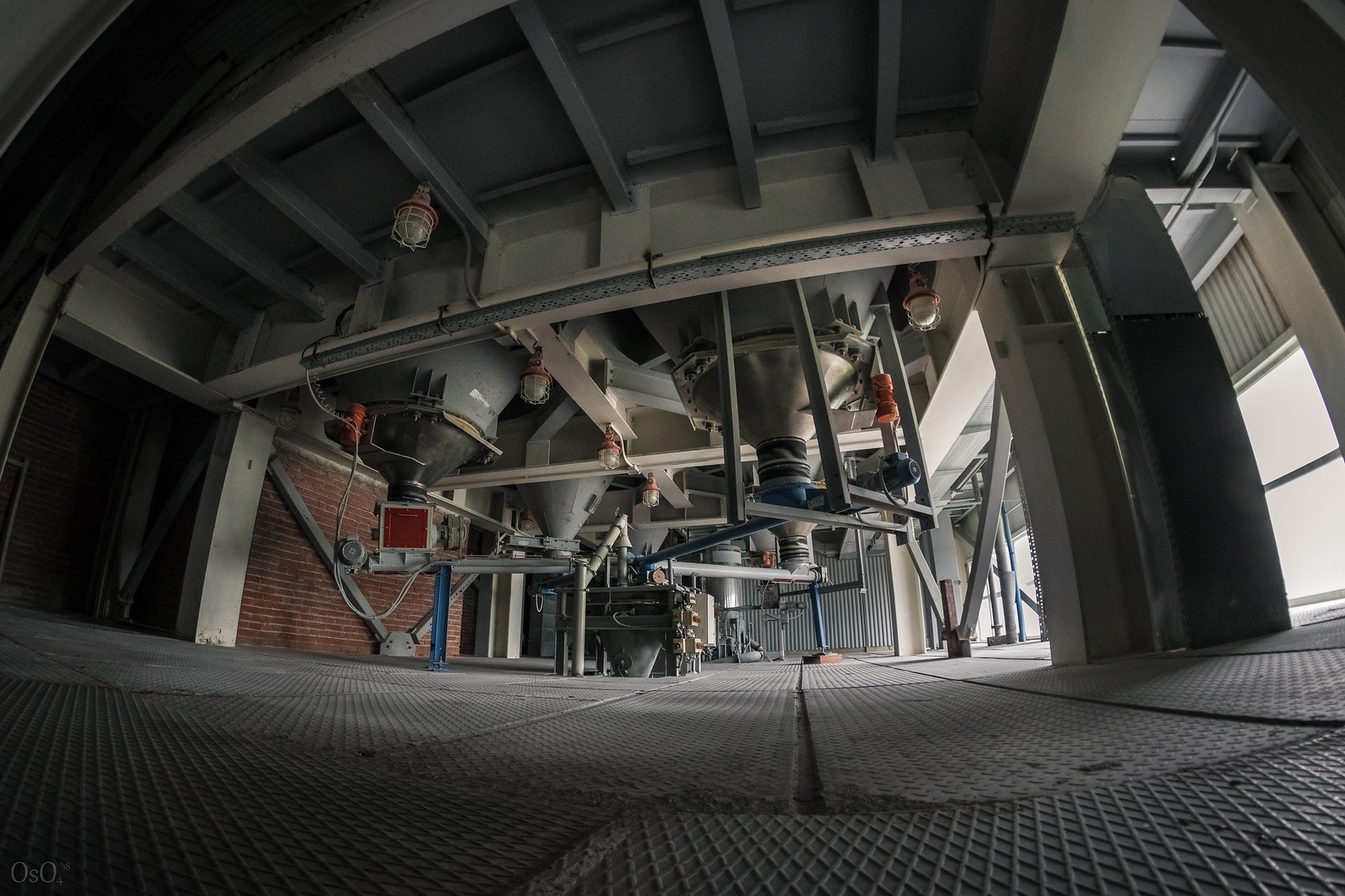
Now the additives. The plant can produce transparent glass as well as blue, red, and brown. For this purpose, there are hoppers with cobalt oxide, selenium, and iron oxide.
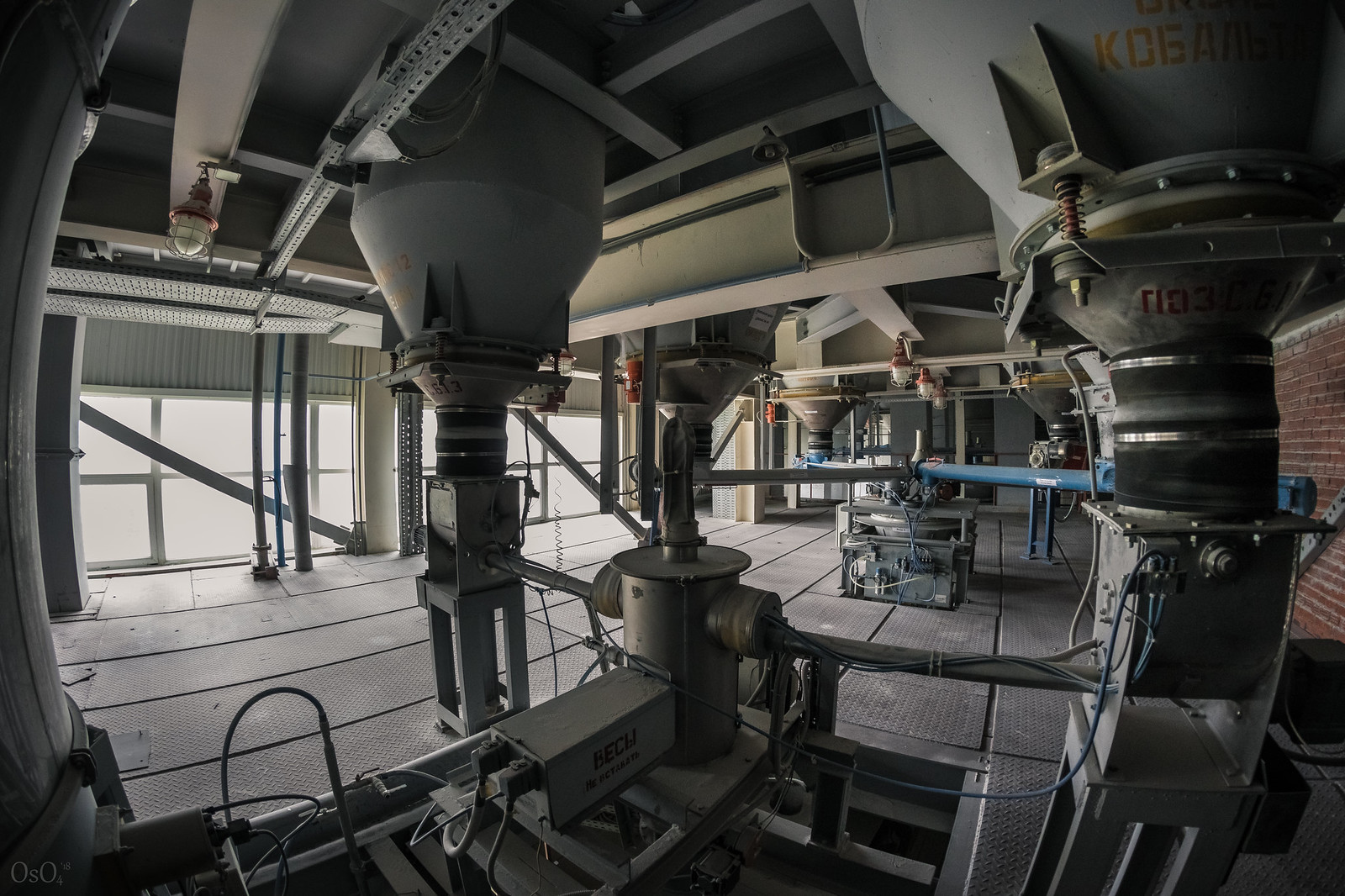
After mixing, the resulting charge is lifted higher, moistened to 4-5% moisture, and goes to bake.
It is moistened here.
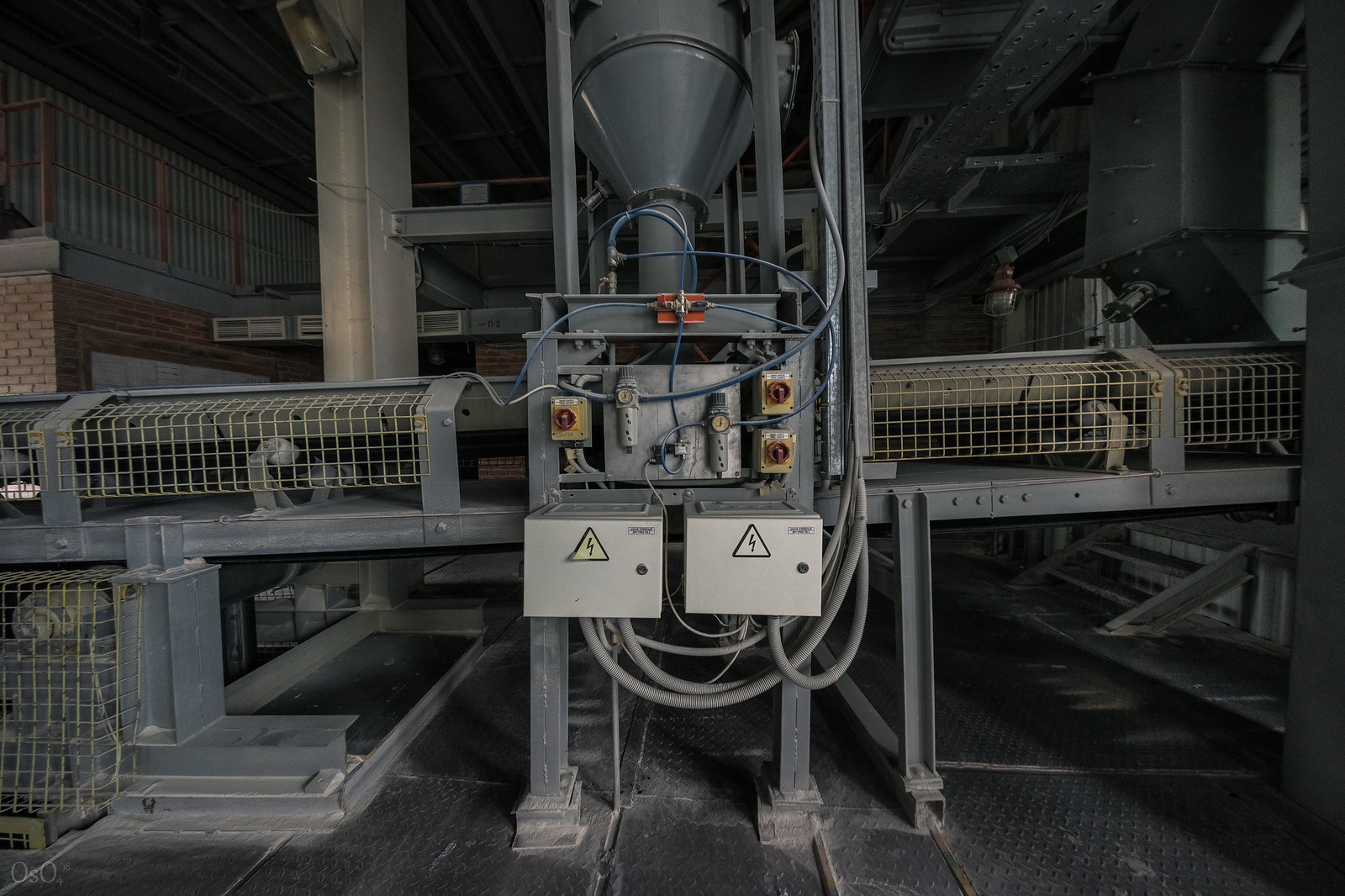
The vertical cylinders drive the mixers in the hoppers. To keep the raw material from flaking, it is sometimes shaken.
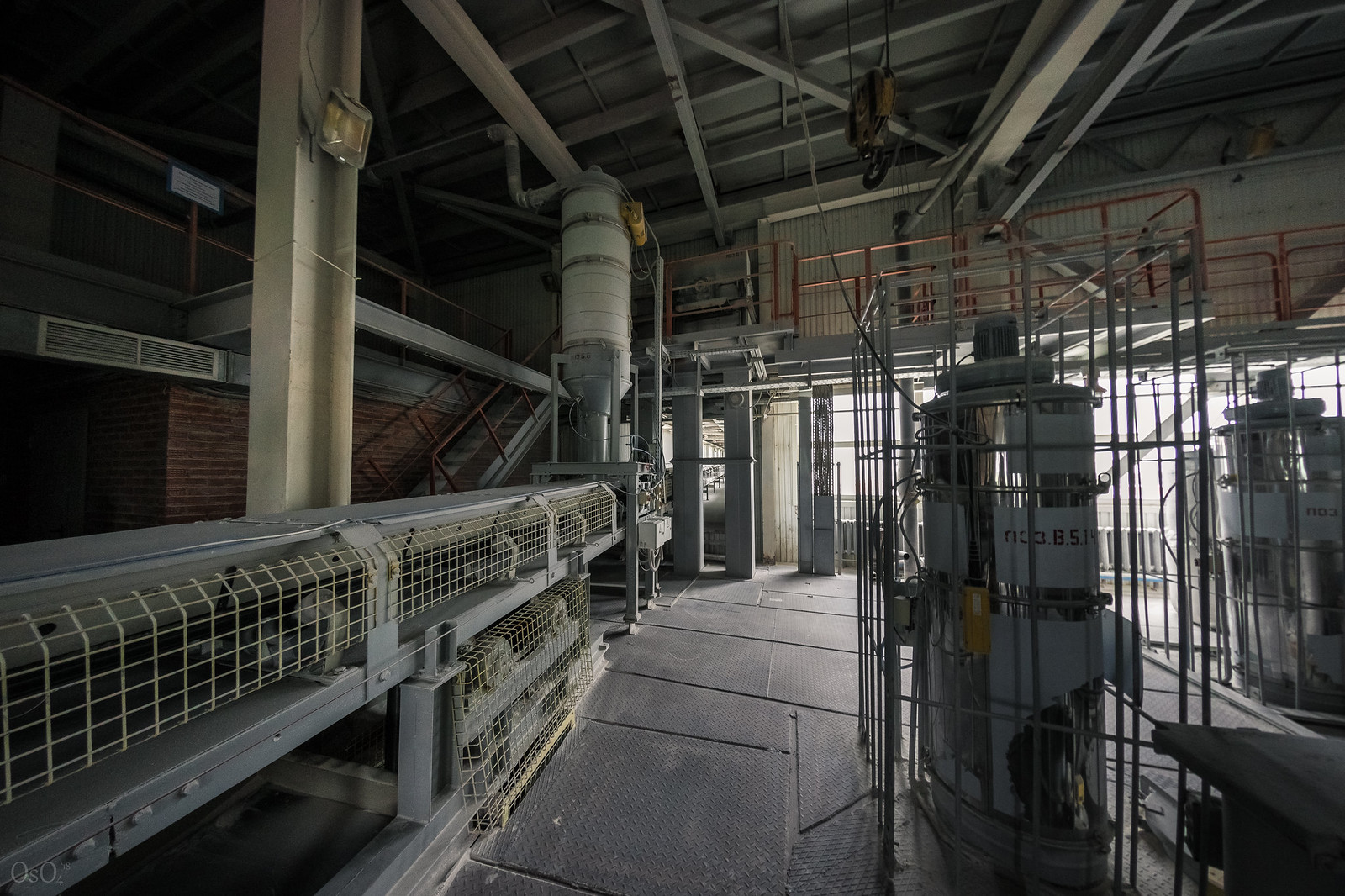
Bags of freshly delivered raw materials.
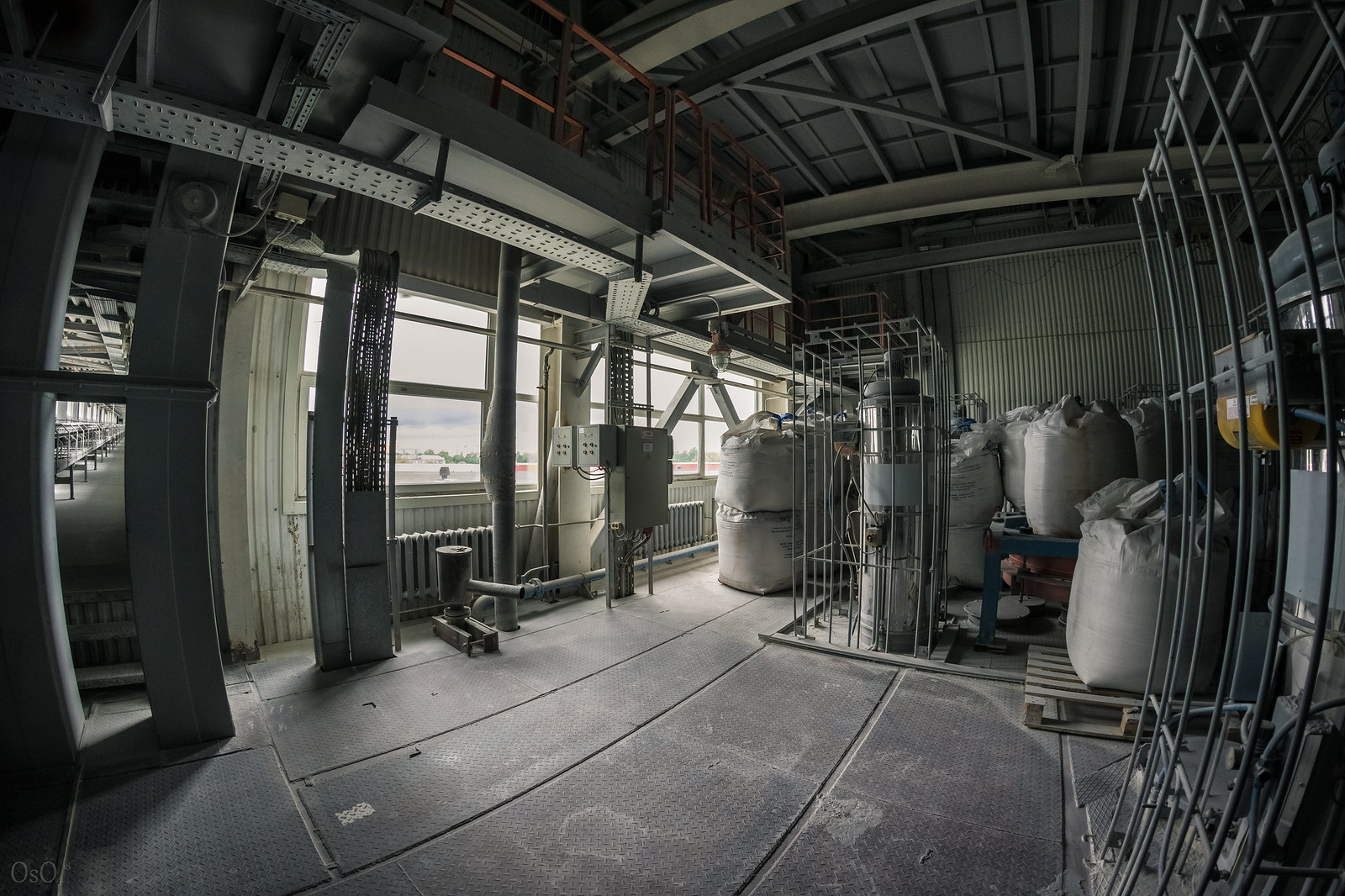
From the storage and preparation shop, the charge moves along a conveyor to the furnace shop.
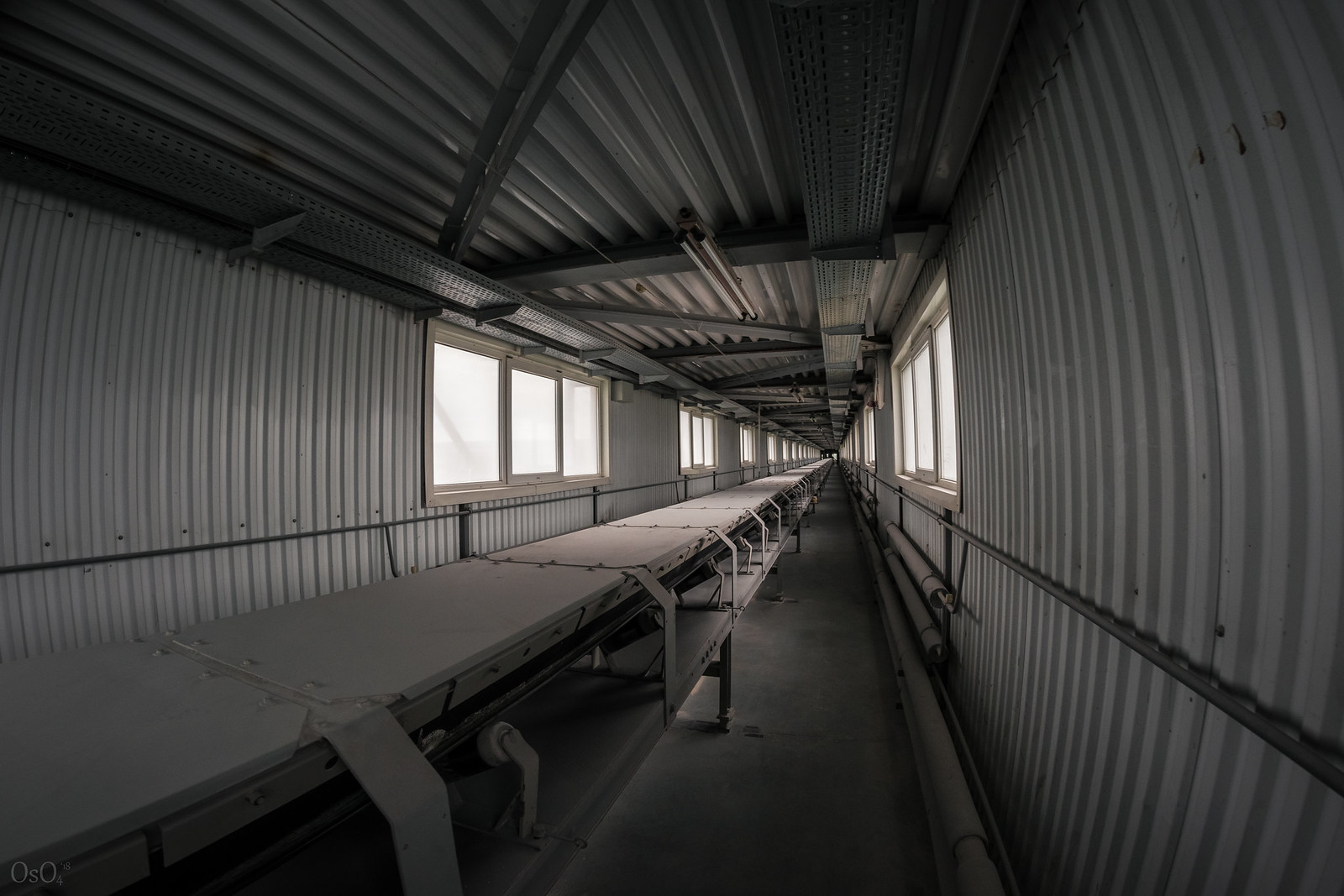
And here is the furnace itself. It looks impressive from up above, especially with the furnace's self-lighting. And it's hot!
This plant has a continuous bath type furnace. As its name implies, inside it looks like a big tub of molten glass. The closer to the working area (where the glass will be molded), the cooler the glass is.

There are also pot-type furnaces (where the furnaces contain pots in which glass is boiled). They are needed for small-scale glass production.
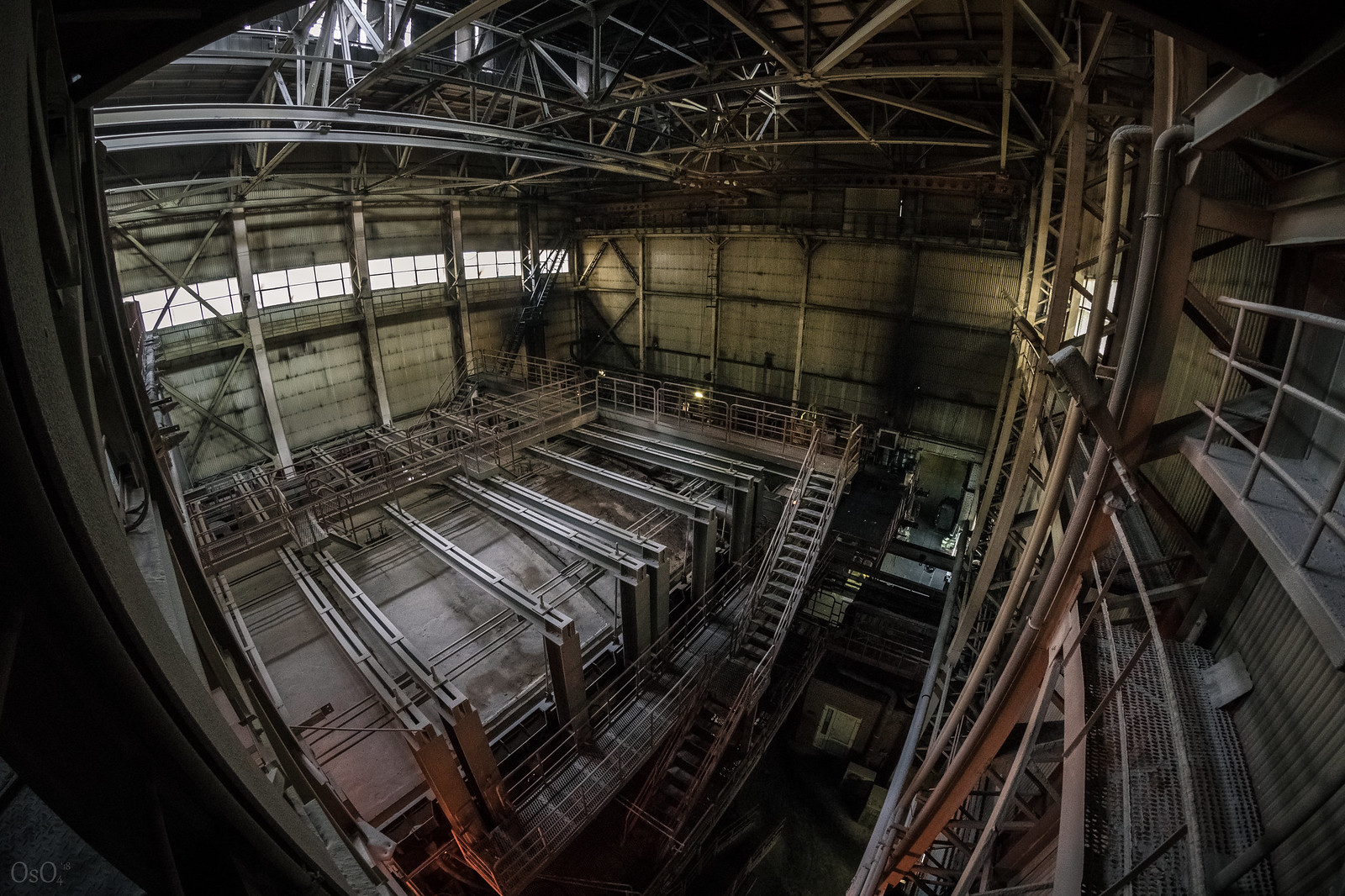
The previous photo shows the main part of the furnace that holds the molten glass. The photo below is the "fuel" part, where there are two recuperators, through which the gas is fed to the main chamber of the furnace, where it burns.
Recuperator is a heat exchanger designed to burn fuel more efficiently. Furnaces use at least two recuperators (as many burners - as many recuperators). The principle of their operation is the following. The hot products of combustion from one burner are sucked through the nozzles of the second burner into the recuperator, heating it. So it goes on for 15-20 minutes (one cycle lasts this long), after which the gas supply is switched from the first burner to the second one, and the combustion products are sucked in through the first one. Since the gas passes through the already heated recuperator, it enters the furnace already heated to 700-800 degrees. Due to this, the gas burns as a whole and saves up to 40% of fuel. After that, the burners are switched again and the cycle repeats.
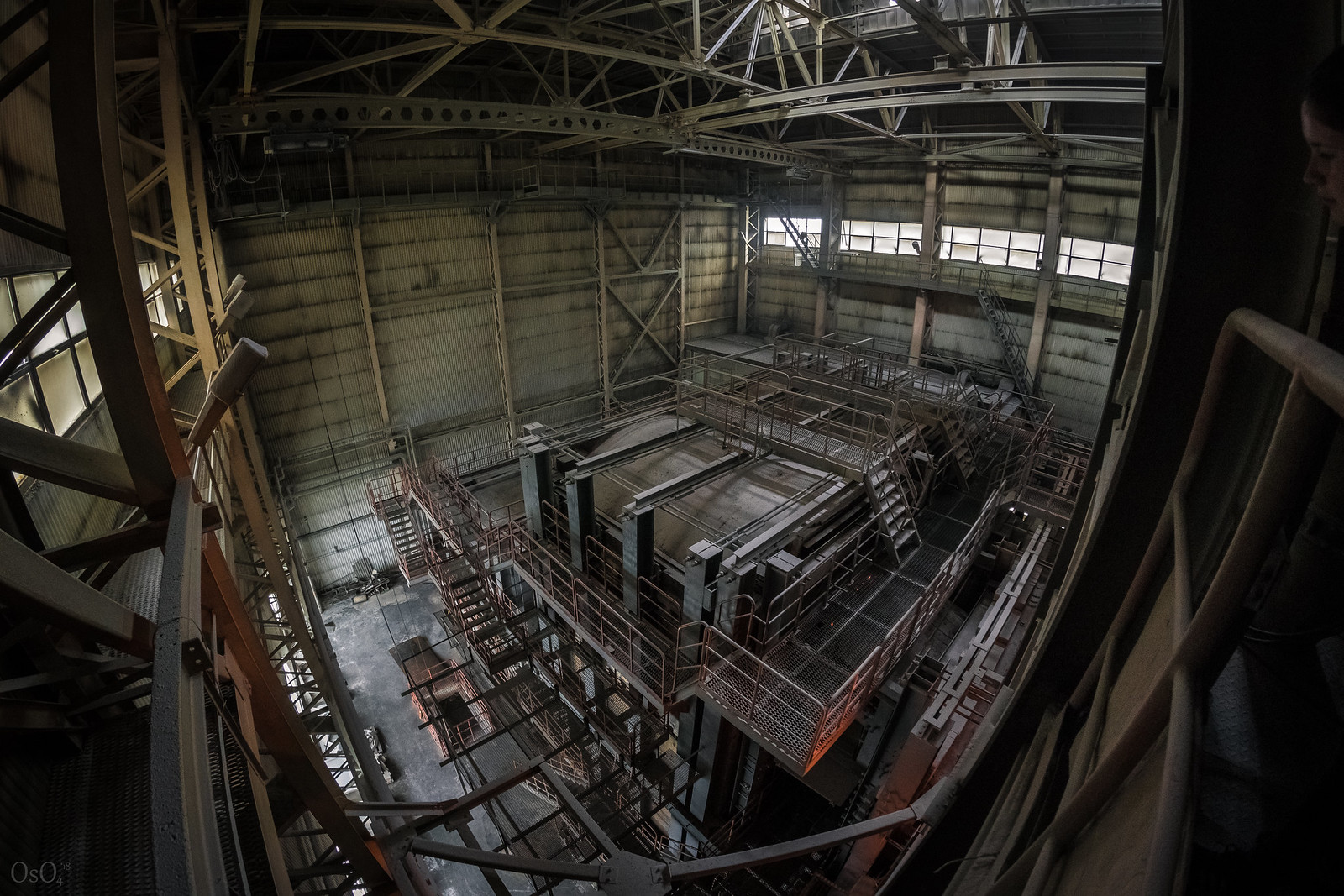
Going down below, you can see different beautiful nifty things.
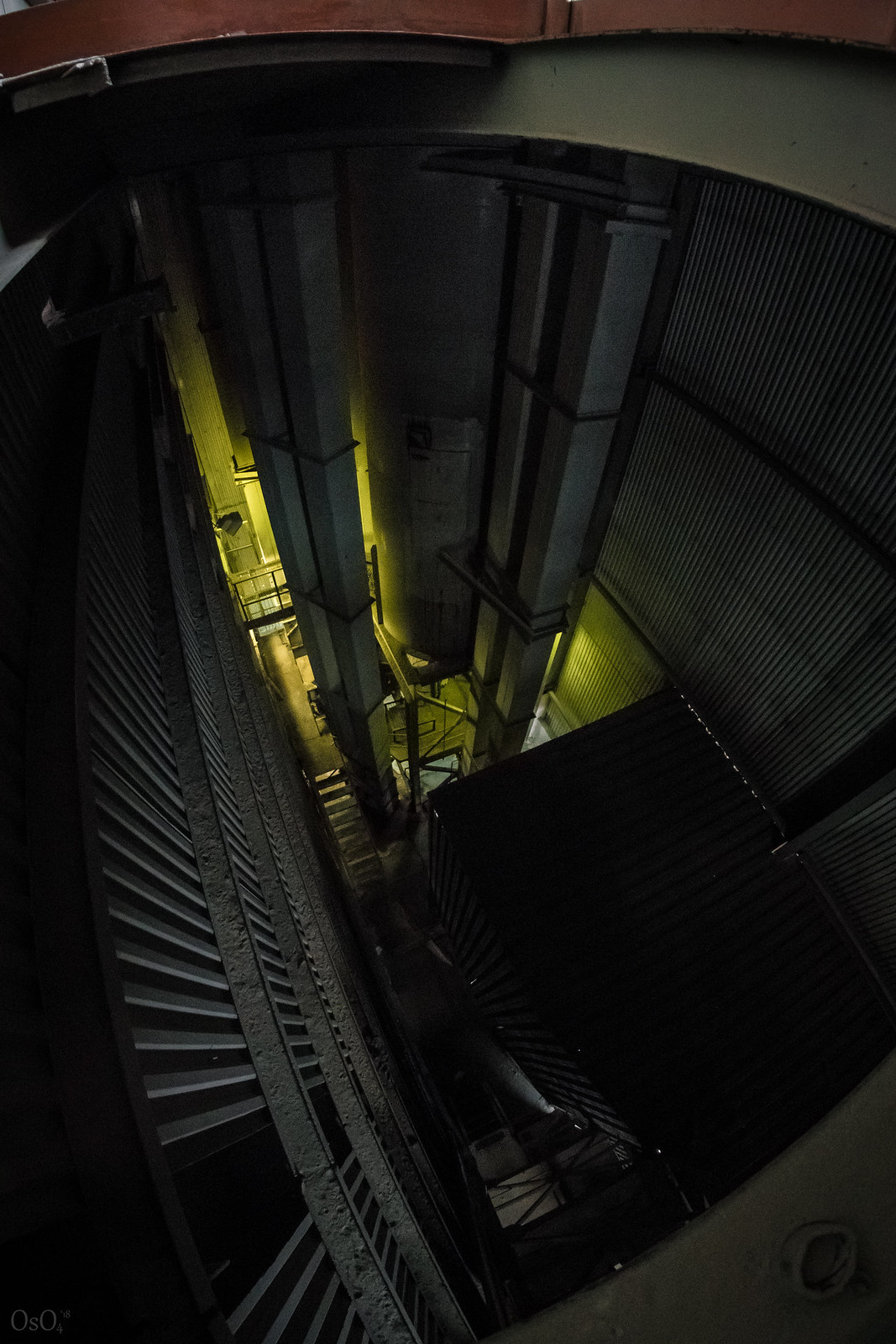
Second floor. From here it is convenient to service the furnace.
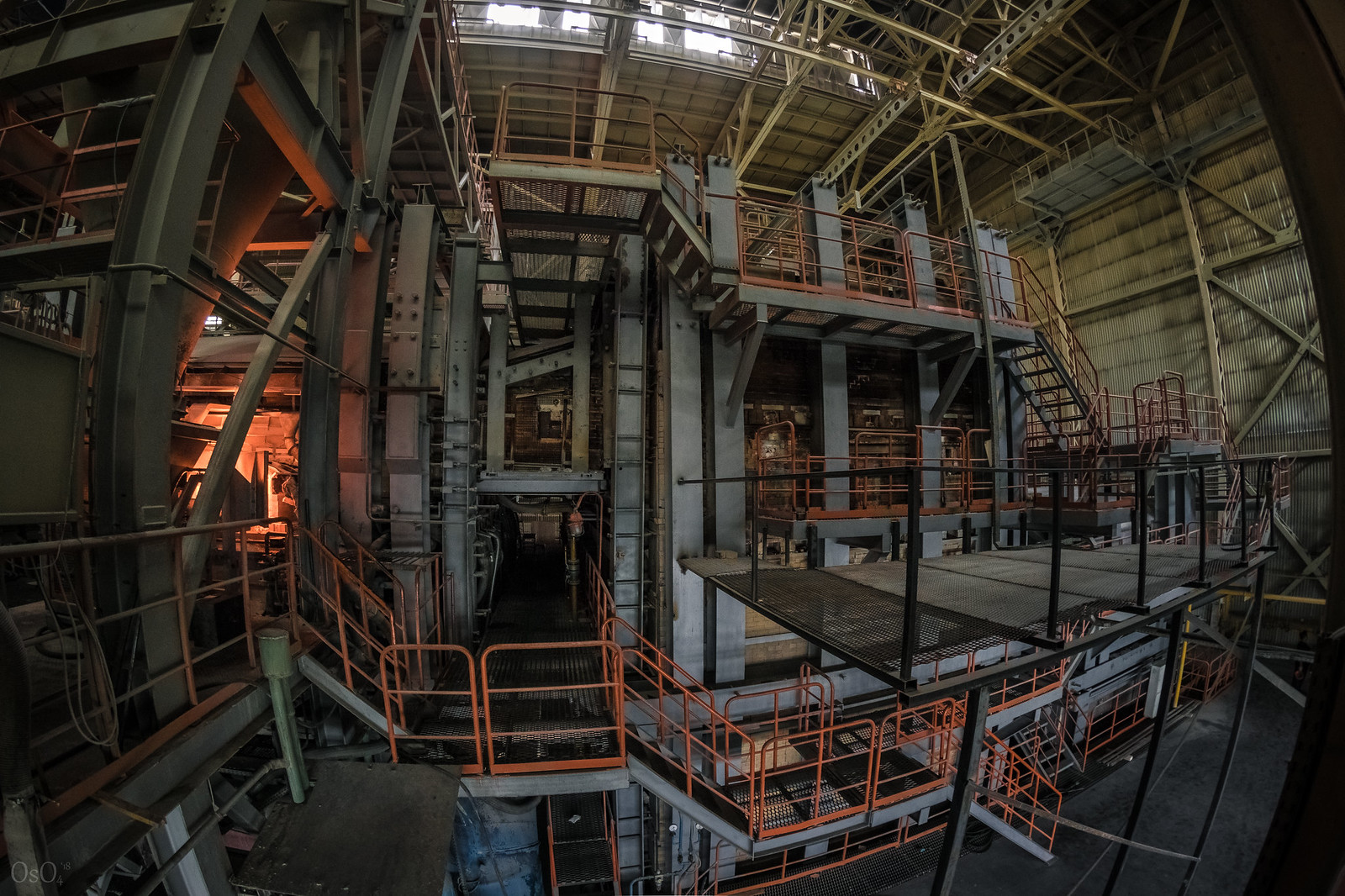
Between the recuperator part and the part with the melt.
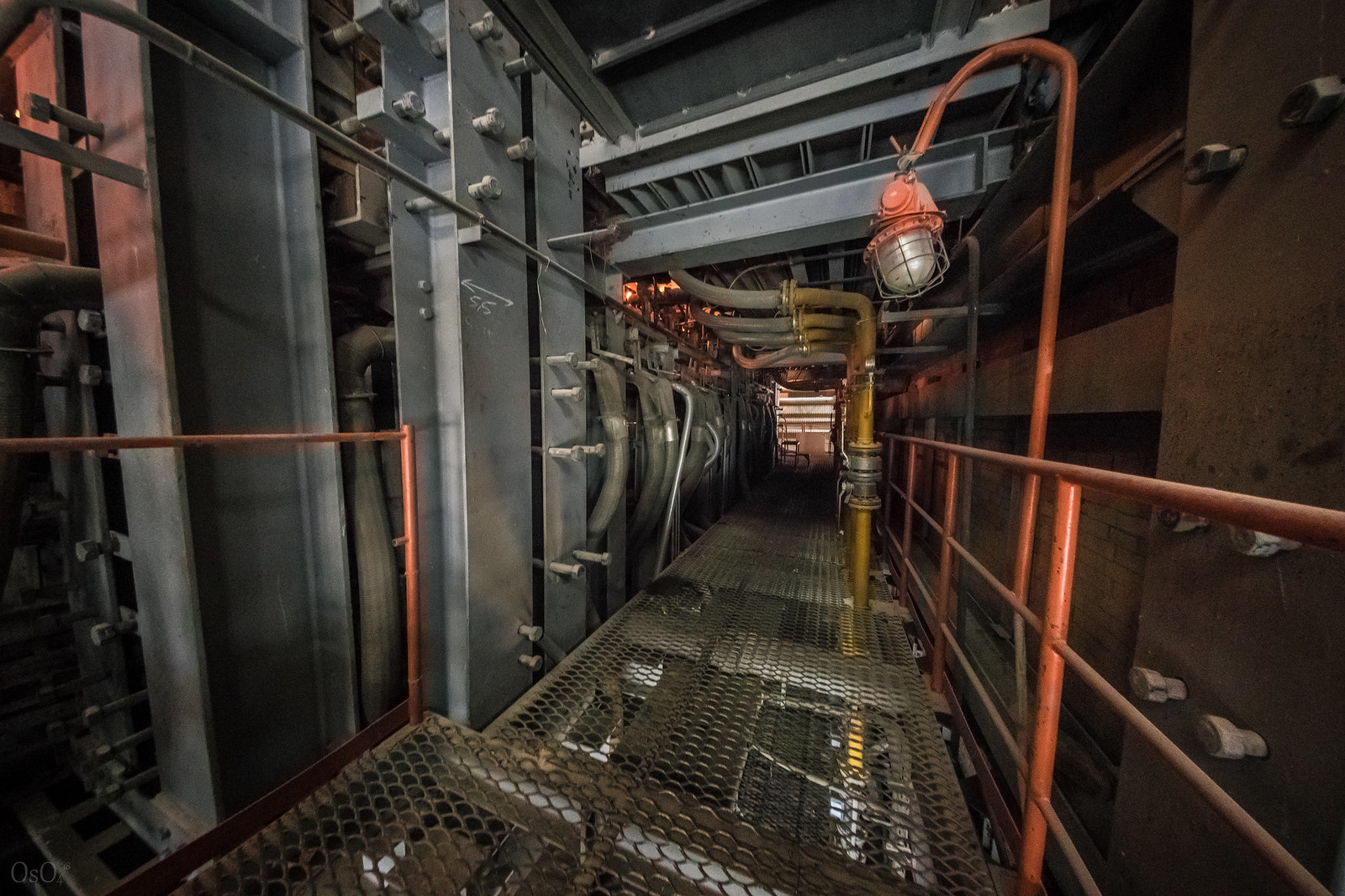
Batch loading.
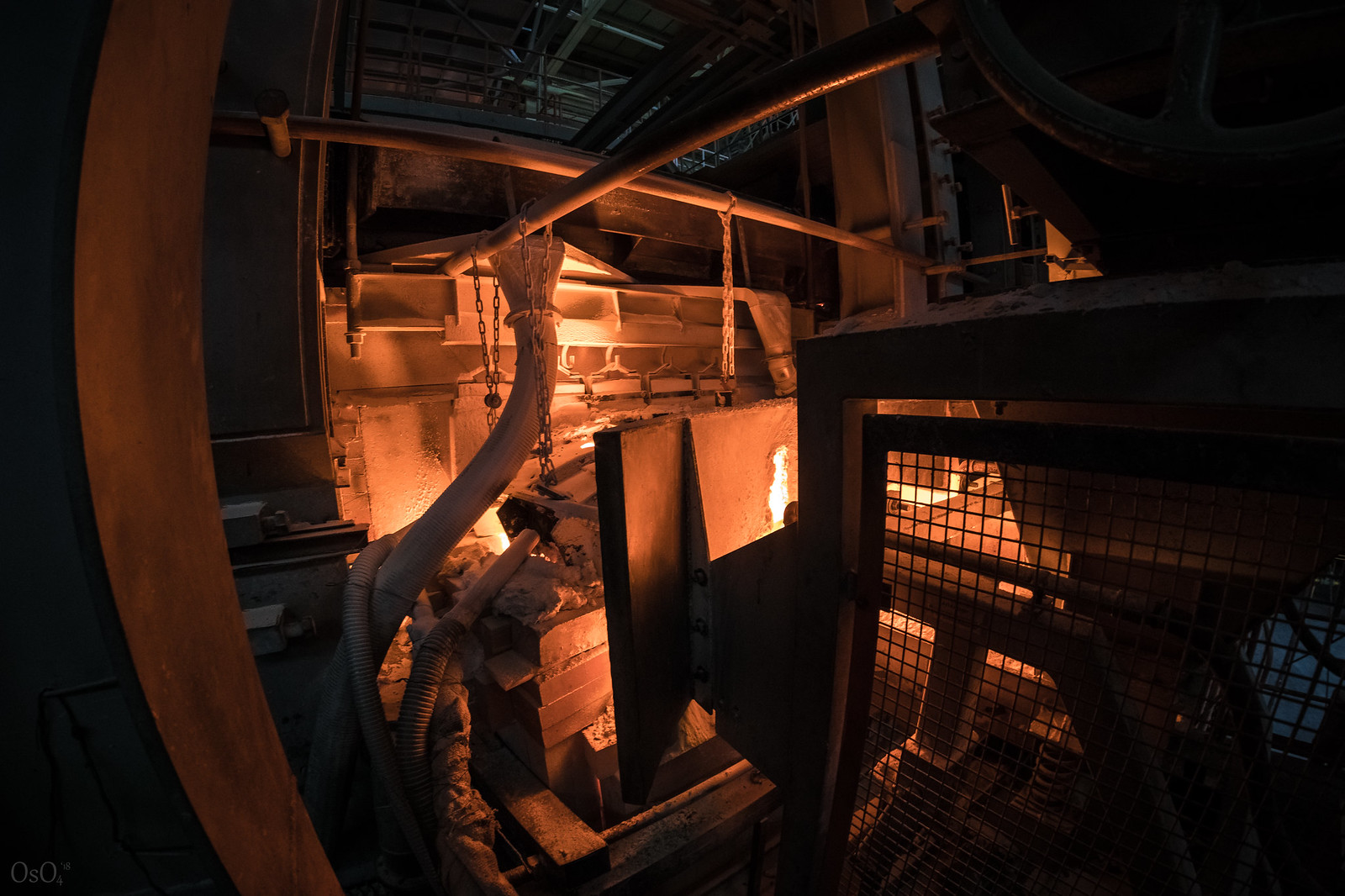
Go down to the first floor.
This is the line to make the glass to be sent to the furnace again. Thus the plant provides itself with glass for the batch.
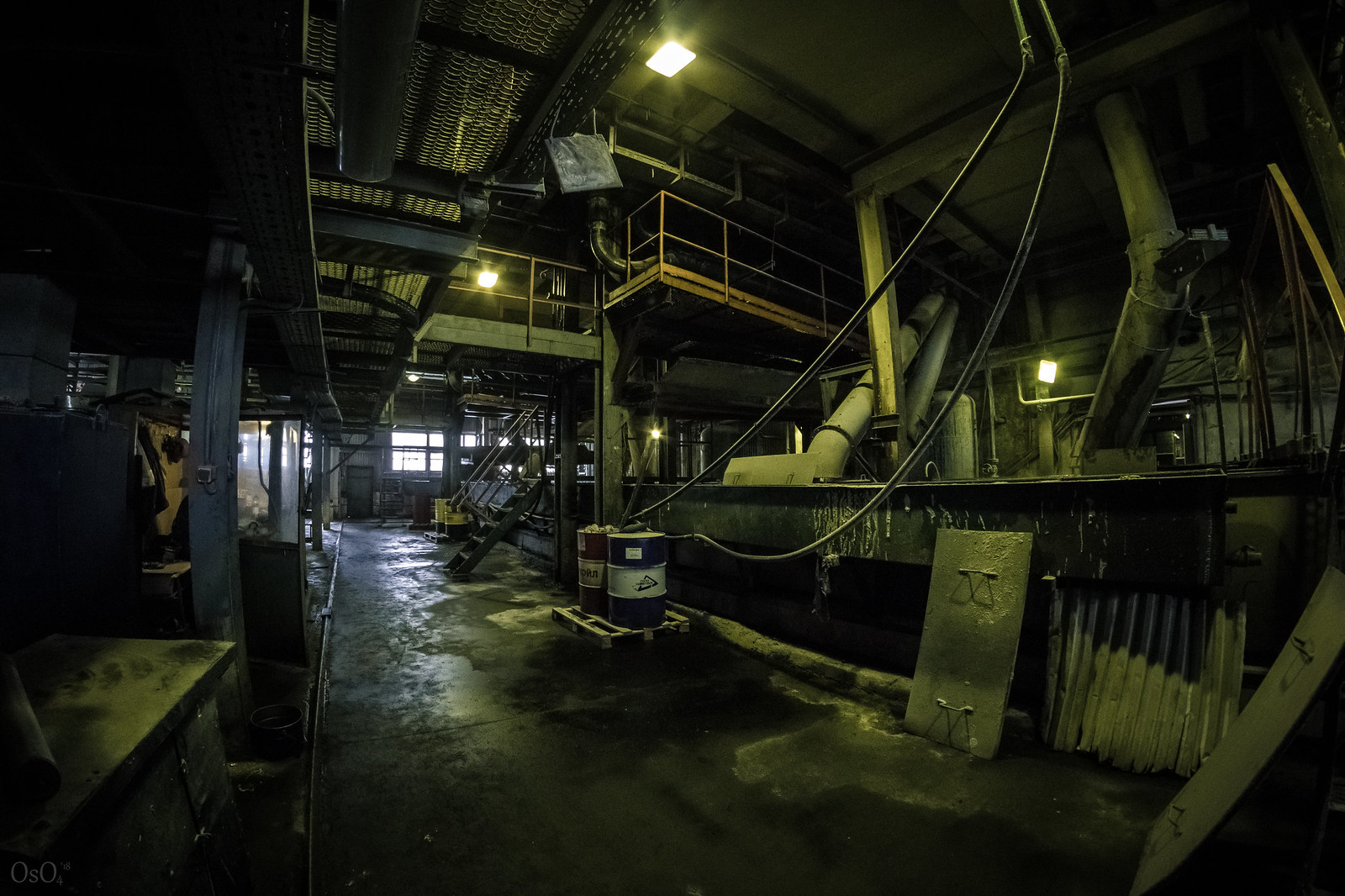
The glass droplets fall into the water, freeze instantly, and float into the receiving containers.
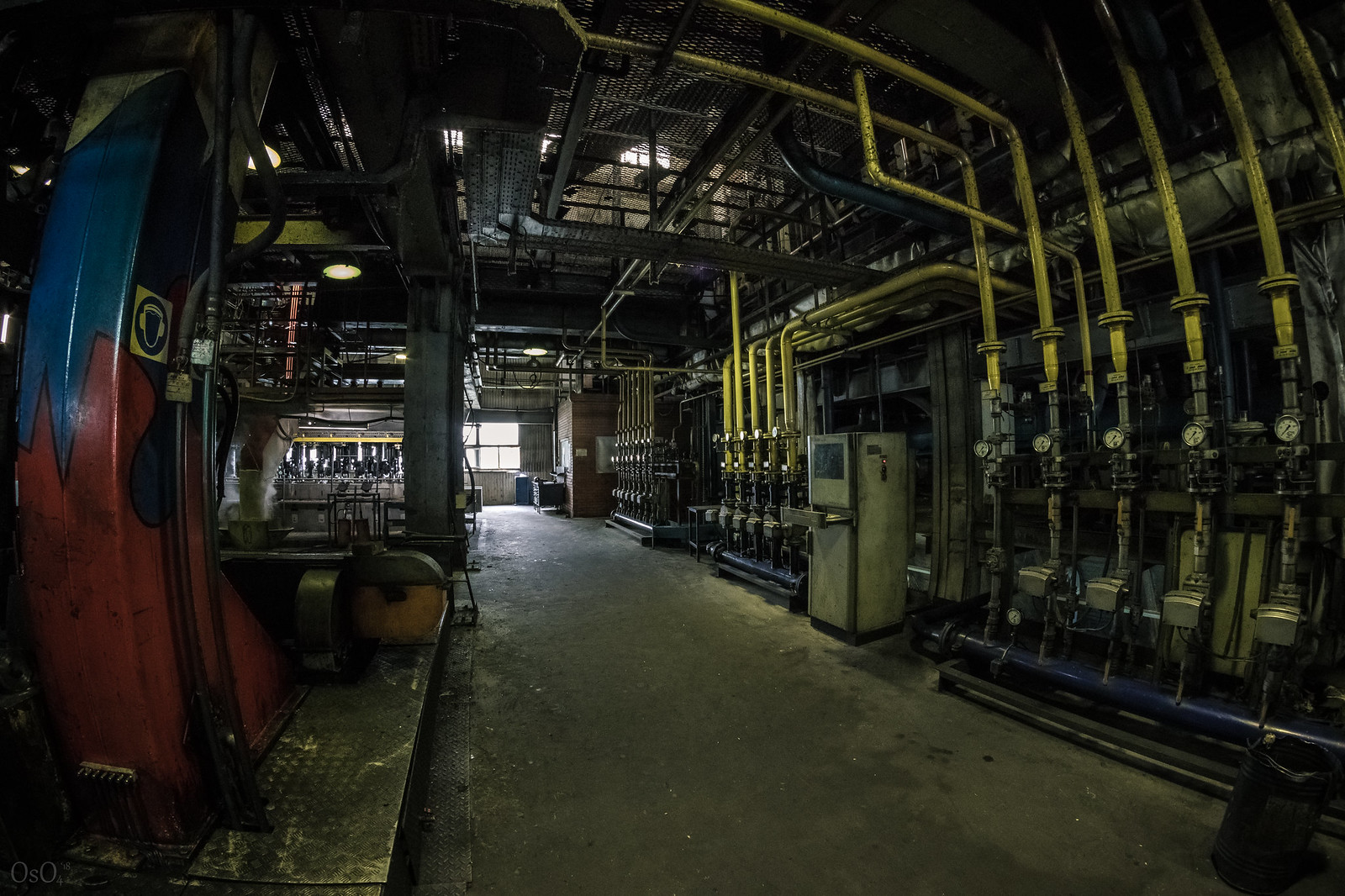
The process of stamping the bottle is a two-stage process. First, a viscous drop of molten metal drops onto the primary mold in the form of a pin and envelopes it. The lower part of the bottle is then clamped by clamping feet, the machine turns the bottle neck upside down, the mold of the finished product is put on top of it, the primary mold is taken out, and then the bottle is inflated until it takes the desired shape. Once the bottle is shaped, the tongs move it to the conveyor.
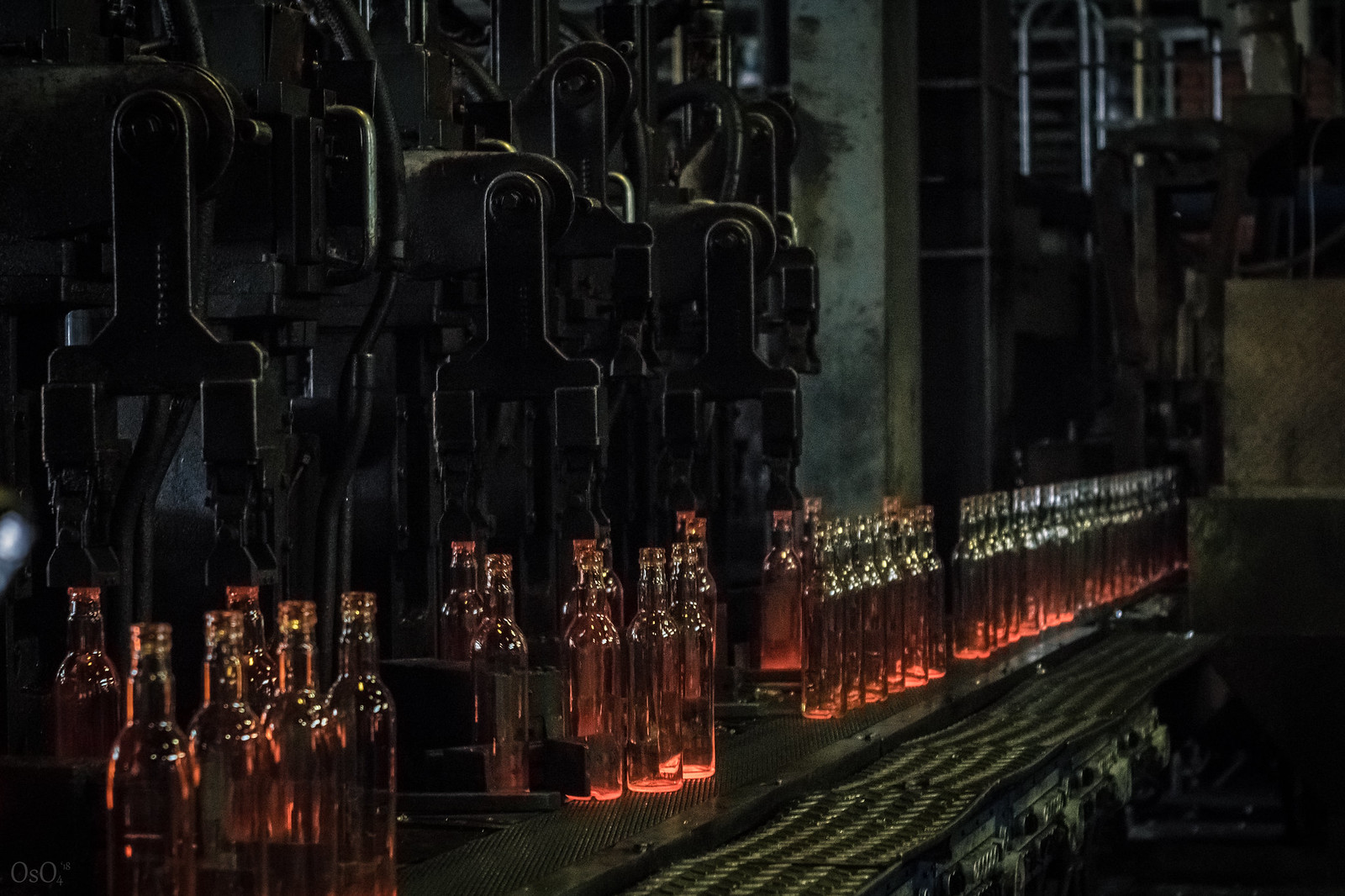
The bottles then proceed to an annealing line (needed to relieve stresses in the glass) and are coated with a protective layer of polymer.
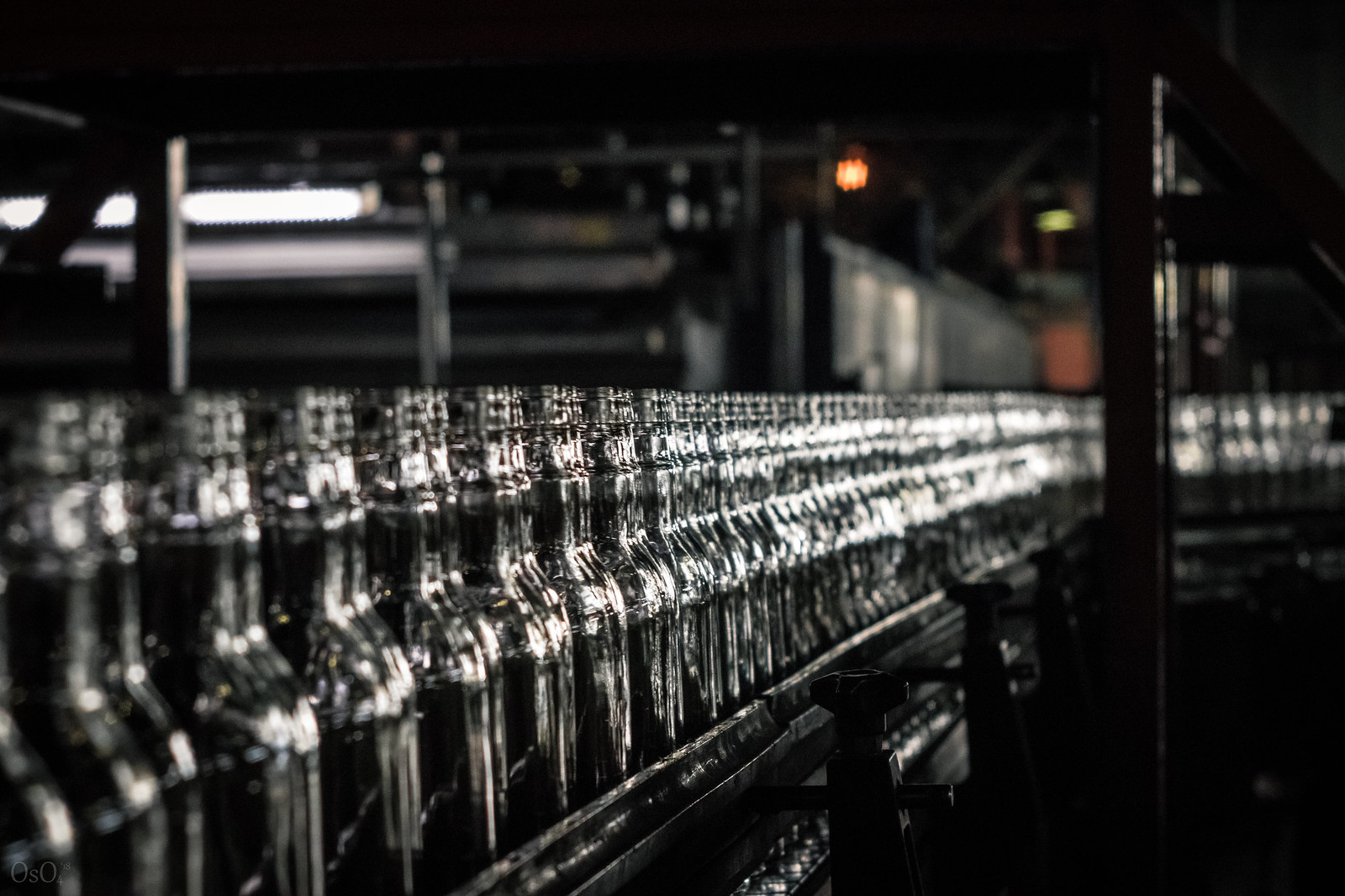
The bottles then undergo quality control. The defective bottles are sorted out.
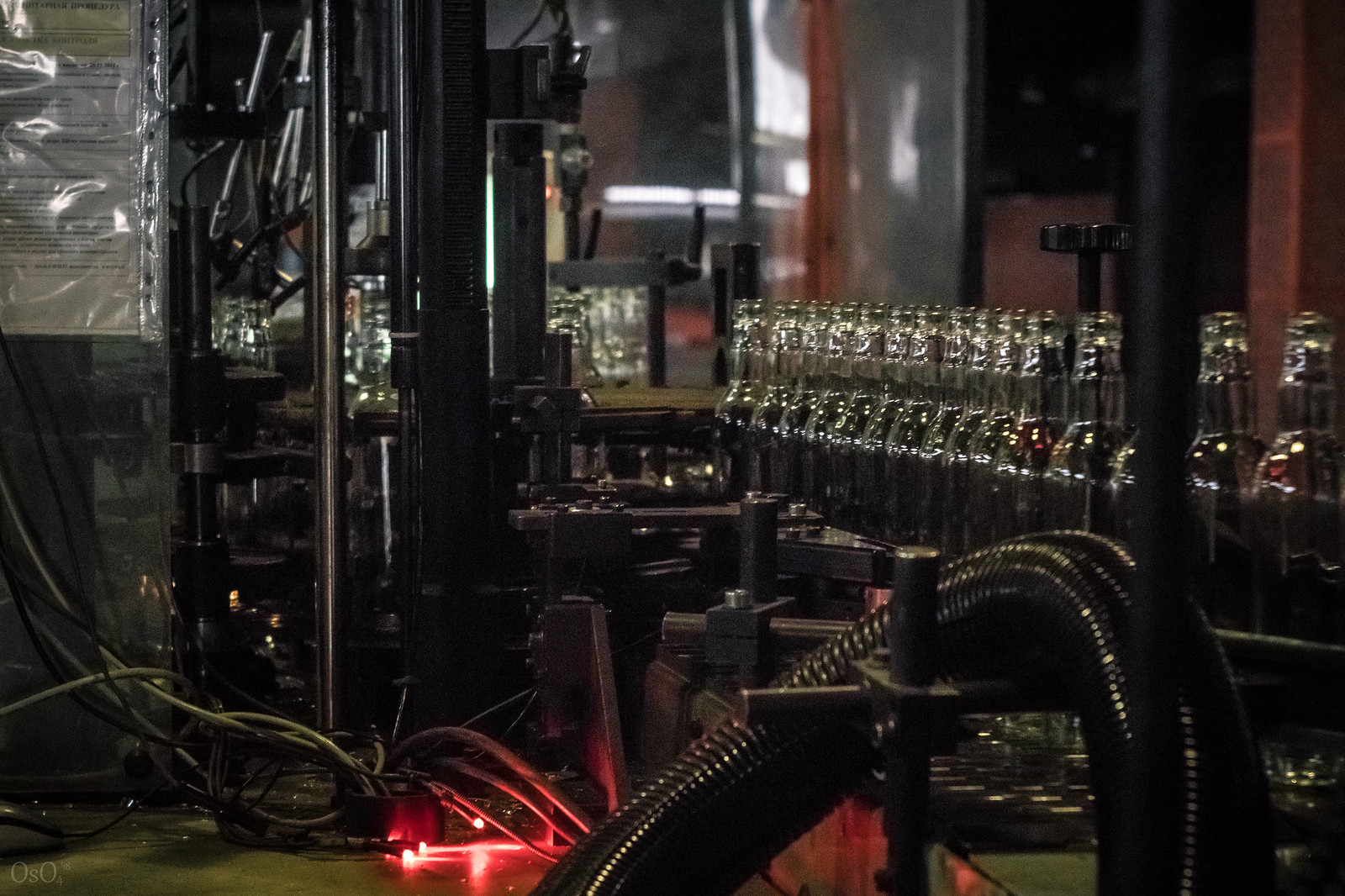
The final stage of production is packaging for shipment to the consumer. Packaging at this plant is fully automatic and goes very quickly. The bottles are first divided into two streams and counted.
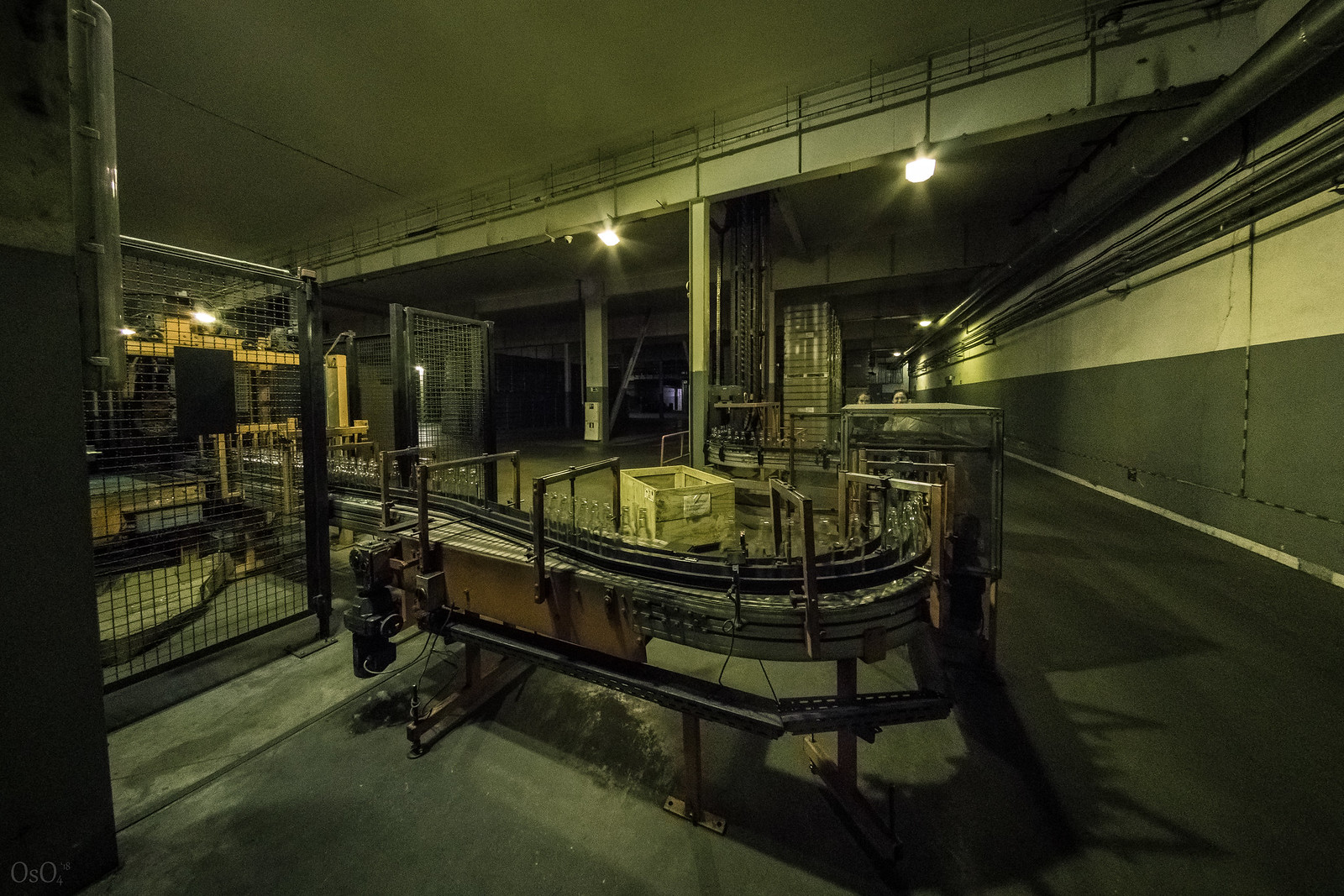
Then they are sent to the packaging machine.
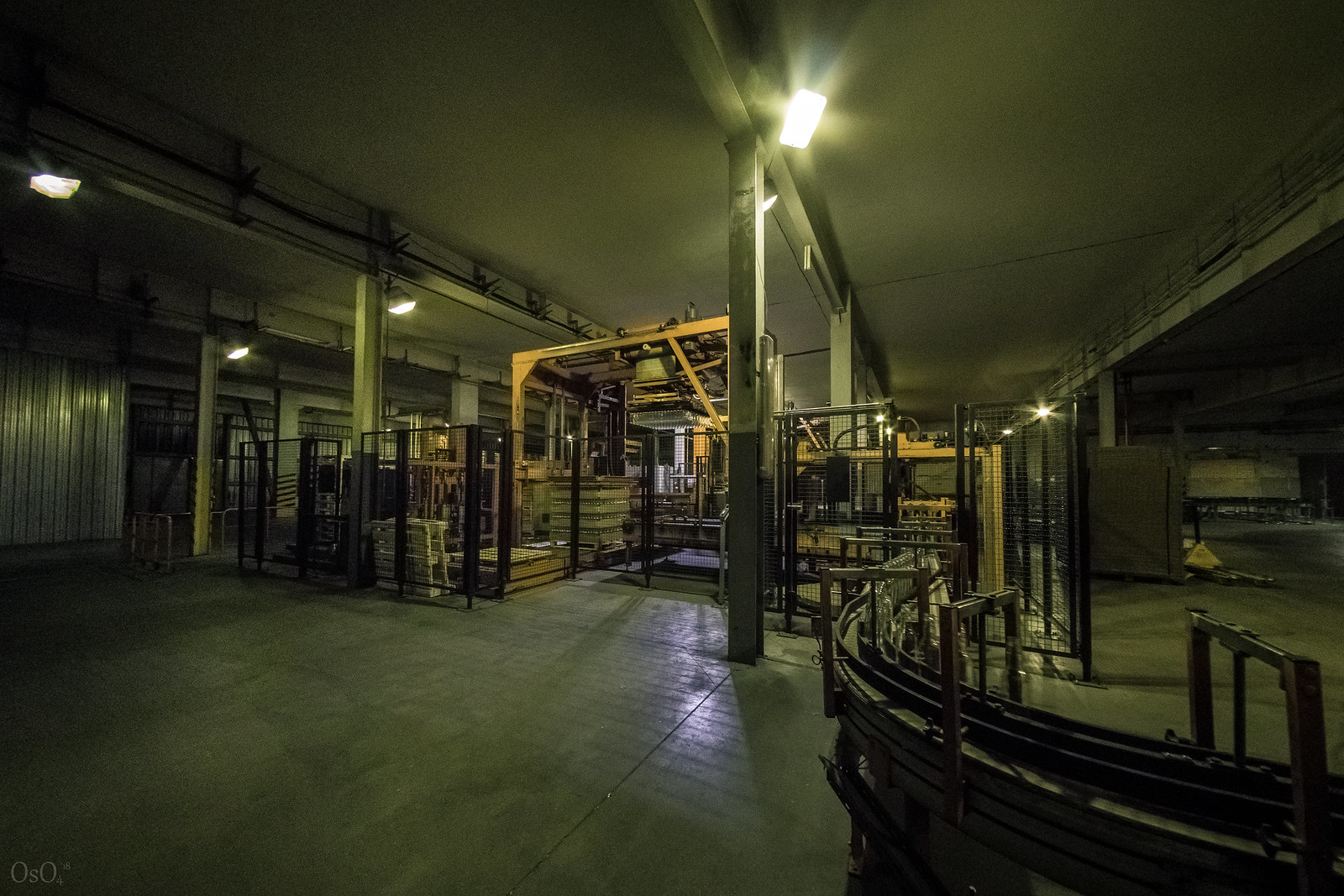
The machine takes a pallet, puts a flange on it, puts the bottles down, and then repeats this operation until it reaches a cube. This cube the machine ships to the warehouse, where a man picks it up on a forklift and takes it to the general warehouse.
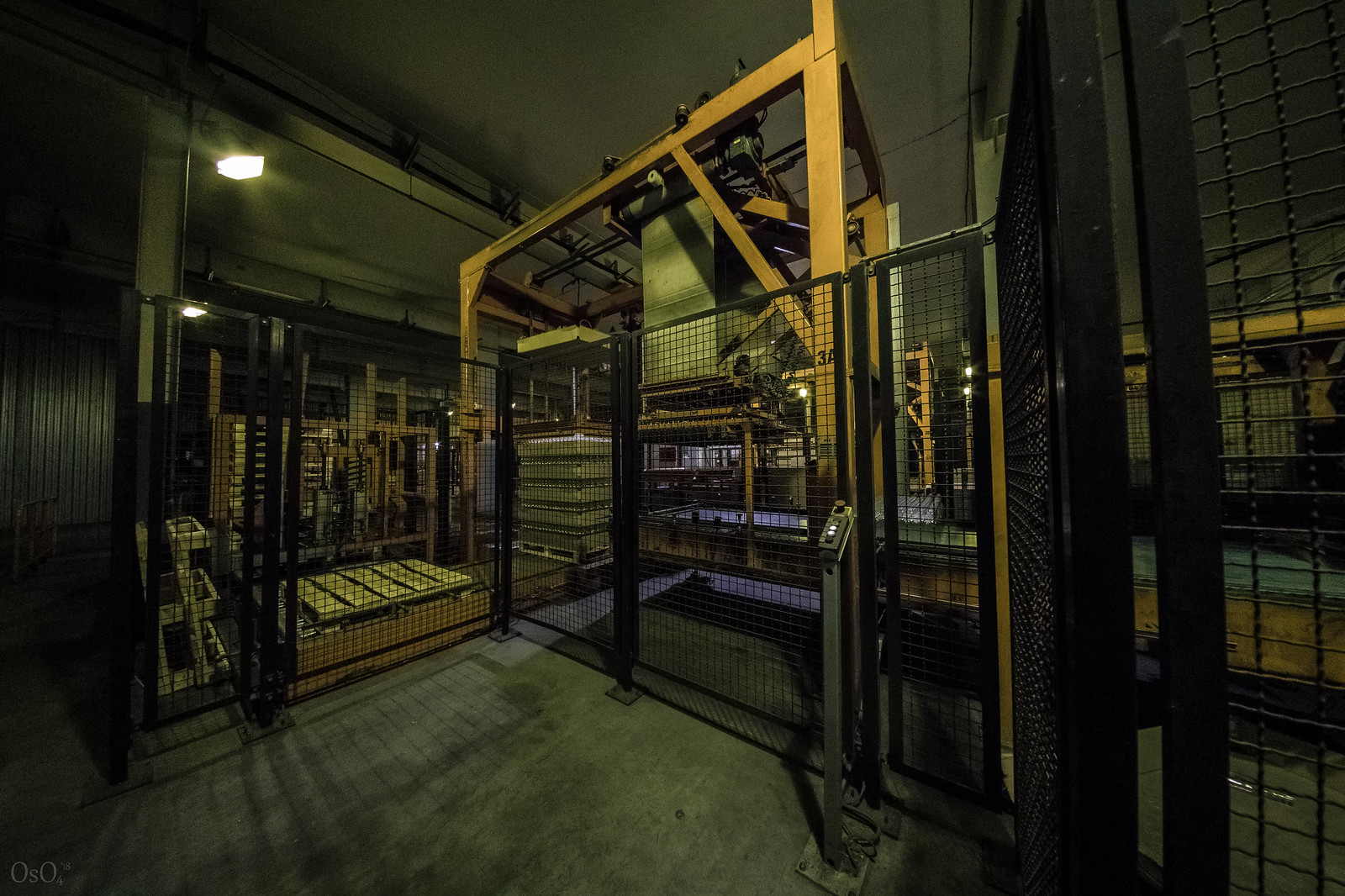
It's just a matter of sending the product to the consumer to fill it with his product. But we'll talk about that some other time :)
No comments:
Post a Comment